Marine vessels face persistent challenges from corrosion, paint degradation, and oil contamination, particularly in confined cabin spaces like ballast tanks and engine rooms. Traditional cleaning methods (e.g., sandblasting, chemical solvents) are inefficient, environmentally harmful, and pose safety risks for crew members. Laser cleaning technology emerges as a groundbreaking solution, offering precision, sustainability, and compatibility with complex marine environments. This article summarizes groundbreaking research on laser cleaning of marine steel EH36, showcasing its effectiveness in removing paint, rust, and oil while preserving material integrity.
- Substrate: Hot-rolled EH36 steel (15mm thickness), a high-strength marine structural steel.
- Contaminants:
- Paint: Black acrylonitrile resin coating.
- Rust: Induced via 3.5% NaCl solution immersion.
- Oil: Wire-cutting fluid applied as a model contaminant.
- Equipment: Pulsed fiber laser system (1064nm wavelength, 350W max power) with robotic motion control
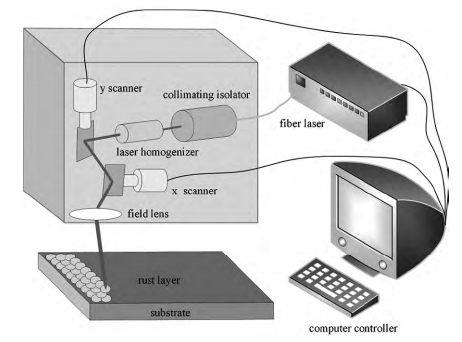
Laser cleaning experimental platform
Through single-factor experiments, optimal laser parameters were identified for each contaminant:
- Paint Removal:
- Parameters: 175–245W power, 350kHz frequency, 300–400ns pulse width, single scan.
- Mechanism: Vibration-induced delamination of paint layers (Figure 6: De-painting macro effect).
- Rust Removal:
- Parameters: ≥175W power, 250kHz frequency, 300ns pulse width, two scans.
- Mechanism: Ablation and melt flow of iron oxides (Figure 10: Post-de-rusting micro-morphology).
- Oil Removal:
- Parameters: 105–175W power, 150kHz frequency, 200–300ns pulse width, single scan.
- Mechanism: Vaporization of organic contaminants
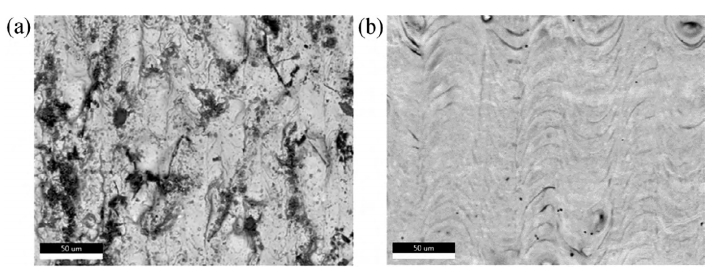
Surface micro-morphology before and after laser degreasing.
(a)Oil contaminated surface;(b) after laser degreasing
Laser Cleaning Process Window for Marine Contaminants
Contaminant |
Scans |
Power (W) |
Frequency (kHz) |
Pulse Width (ns) |
Paint |
1 |
175–245 |
350 |
300–400 |
Rust |
2 |
≥175 |
250 |
300 |
Oil |
1 |
105–175 |
150 |
200–300 |
- Post-cleaning Elemental Reduction:
- Paint: C content dropped from 69.57% to 18.94%; N/O nearly eliminated
The surface element content without laser de-painting(Wt %)

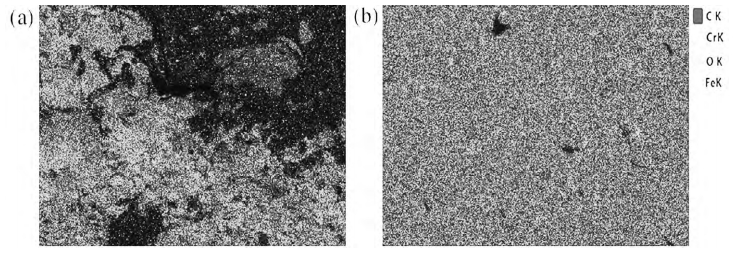
Surface element distribution before and after laser de-rusting. (a) Corroded surface; (b) after laser de-rusting
- Hardness Enhancement:
- Rust removal: +20HV (max).
- Paint removal: +13HV.
- Oil removal: +3HV
Surface hardness before and after laser cleaning
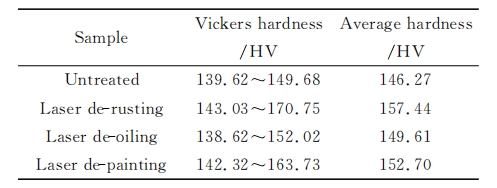
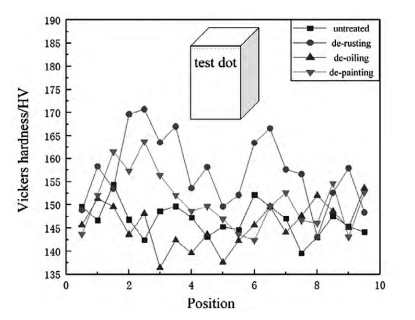
Vickers hardness of the substratebefore and after cleaning
- Tensile & Bending Strength:
- No significant changes post-cleaning , confirming non-destructive nature.
Yield strength and tensile strength of the substrate before and after laser cleaning
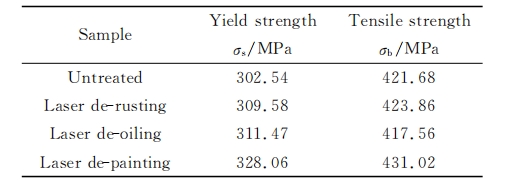
Maximum load and bending strength of bending test
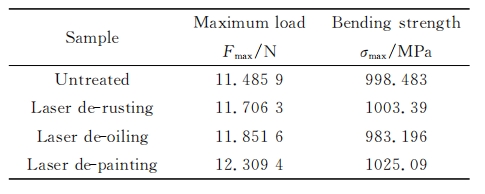
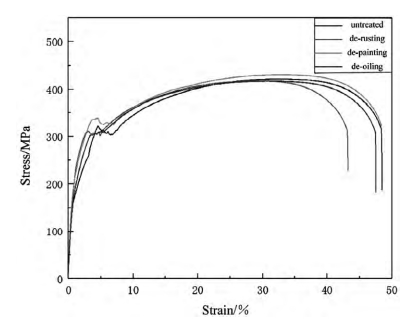
Stress strain curves of different cleaning samples
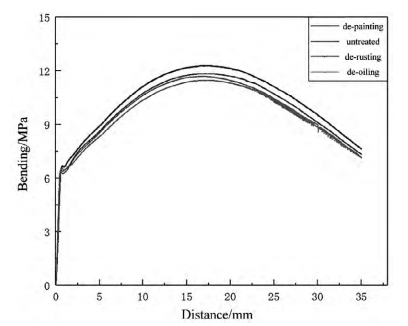
Bending stress curves of different cleaning samples
- Environmental Friendliness: No chemicals or abrasive waste, aligning with IMO 2020 regulations.
- Precision: Targeted removal of contaminants without damaging substrate (critical for thin-walled ship structures).
- Efficiency: Single-pass cleaning for paint/oil; dual-pass for rust, far faster than manual methods.
- Safety: Remote operation reduces crew exposure to hazardous environments.
This study paves the way for laser cleaning in:
- Shipbuilding: Pre-painting surface preparation.
- Maintenance: In-cabin cleaning of oil tanks and ballast tanks.
- Retrofitting: Eco-friendly removal of lead-based paints in older vessels.
Future research may focus on scaling to larger surfaces, integrating with AI-driven robotic systems, and optimizing energy efficiency for offshore applications
Laser cleaning technology offers a transformative solution for marine maintenance, combining environmental sustainability with industrial-grade performance. By optimizing parameters for different contaminants, this method ensures efficient, non-destructive cleaning, making it ideal for the rigorous demands of global shipping. As the industry shifts toward greener technologies, laser cleaning is poised to become a standard practice in maritime surface treatment.